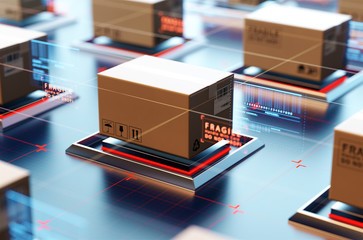
Introduction
The past years have shown the vulnerability of the supply chain. Just-in-time inventory philosophies have fallen short and resulted in lost site supply for warehousing and distribution centers, and the post-COVID consumer is more conscious of their decisions. The risk of the next disruption is just around the corner. Success in 2023 will depend on the success of supply chains, and one-third of company leaders believe their supply chain distribution problems will last through 2023 (SAP News).
The evidence is clear; supply chain leaders will face great uncertainty in the coming year. However, cross-global fulfillment will largely depend on the ability of warehouse and distribution centers to manage operations proactively. Furthermore, the decline in revenue, which will affect 58% of companies, will continue to undermine the efficiency of fulfillment strategies. Let’s look at how supply chain parties can improve warehousing and distribution in global fulfillment and distribution in the coming year.
Optimize Labor
Optimizing labor resources is the most common facet of cross-global fulfillment in 2023. According to Supply Chain 24/7, the continuous process of doing more with less and hiring more people to meet demand is inevitably facing a crossroads. A tightening labor market will mean that “warehouses that rely heavily on manual processes will be way behind the curve, and even those that still rely on outdated technology and legacy systems will struggle. However, advanced warehouse management systems, voice picking, light picking, and robotics can help fulfillment houses do more with less labor.”
As a result, the need to do more with less will become more integral to figuring out the best way to leverage resources and avoid overspend. Further, today’s supply chain professionals will face the persistent problem of defining what’s necessary and what could be over the next year. Thus, the best way forward will be to redefine operation standards and focus on tracking labor metrics that foster innovation and supply chain optimization.
Stay Flexible With Multi-Location Inventory Management
Another core strategy for success in warehousing and distribution will revolve around inventory management. According to UpKeep.com, the overwhelming majority of companies, 75%, are proactively looking to find ways to improve inventory management practices (UpKeep). Unlike a single-site supply inventory strategy, multi-location inventory management leverages all existing spaces down to the store level.
Using a centralized system that can visualize all activities and inventory needs is crucial. This central supply chain control tower ensures all companies can keep operating at peak capacity without breaking the bank.
Further, there may be instances where the success of the supply chain hinges on the reallocation of inventory between individual stores and distribution centers to fill more orders. Reducing the total volume and leveraging more space across multiple locations conserves resources (Rickerby).
Build New Fulfillment and Cross-Global Partnerships
The best partnerships should put your brand front and center. New fulfillment partnerships are a great way to leverage the sustainable and forward-looking premise of other brands as your own. This may also include leveraging additional site supply resources to avoid stock-outs and enhance cross-global warehousing and distribution. These partnerships demonstrate your commitment to a better future and will effectively boost your customers’ views of your brand. Plus, they reduce your total risk and costs along the way.
Improve Packaging
Any conversation on better warehouse distribution and fulfillment is complete with discussing packaging design and the ease of shipping. Poor packaging will upset customers and, even worse, additional waste. With 72% of American consumers saying that product design packaging influences their buying decision, it is no surprise that there is a marketing effort to make the outside of a box more appealing (Packaging Fulfillment Co., Inc).
Regardless, the message is still the same. Customers want eco-friendly materials and minimalist designs. Those facts allow customers to feel good about their purchases and how such purchases affect the global economy. That’s not to say that your brand cannot be evident on the package. Your brand should be apparent, but your message will reverberate beyond the package. It should indicate your commitment to sustainability and give rise to your need for a better tomorrow. In other words, be present, but do not go overboard. Provide the just-right level of packaging and ensure that your packaging is recyclable.
Prioritize the Customer Experience
Supply chain leaders who want to improve cross-global fulfillment, warehousing, and distribution must prioritize the customer experience. According to 2023 survey results, 45.9% of companies rate customer experience as the number one priority for the next five years, surpassing pricing and product (SuperOffice). Greater customer experiences have a self-propagating effect that will generate more demand for your e-commerce brand and reduce the confusion of fulfillment in the first place.
Choose ModusLink to Streamline Your 2023 Fulfillment Strategy
The right strategy for global warehousing and distribution in 2023 is not finite. Today’s supply chain leaders need a continuously evolving strategy to meet customers and do more with less. Fortunately, those that care can understand their supply chains and where to do more and less. Connect with an expert in global fulfillment to learn more about the value proposition of working with ModusLink today.
Bibliography
Packaging Fulfillment Co., Inc. 5 Custom Packaging Trends for 2023. n.d. 29 November 2022. <https://www.packagingfulfillment.com/5-custom-packaging-trends-for-2023/>.
Rickerby, Matt. How to Improve Your Multi-Location Inventory Management. 10 November 2022. 29 November 2022. <https://www.extensiv.com/blog/multi-location-inventory-management>.
SAP News. New Research Forecasts the State of U.S. Supply Chains in 2023. 24 October 2022. 02 December 2022. <https://news.sap.com/2022/10/us-supply-chains-in-2023-new-research-forecast/>.
SuperOffice. 32 CUSTOMER EXPERIENCE STATISTICS YOU NEED TO KNOW FOR 2023. 15 November 2022. 2 December 2022. <https://www.superoffice.com/blog/customer-experience-statistics/>.
UpKeep. What are the most interesting stats and facts about inventory management? n.d. 4 December 2022. <https://www.upkeep.com/learning/inventory-management-stats>.